Every operator hates to break the tap. Removing a tap without damaging the parts is a painful task. In addition, tapping processing belongs to precision machining and is usually the final process of processing. This means that the breakage rate of the tap may determine the scrap rate of the product. Excluding the cost of using a single tool, the qualification rate of tapping will determine the comprehensive cost of the tool. What are the main reasons may caused tap breakage over there? If the tap is broken, it cannot be separated from below seven reasons

1. Choose the right bottom hole diameter
Tapping the bottom hole with a tap requires matching the size of the bottom hole. Generally, the corresponding range of bottom hole sizes is provided in the catalog. Please note that this is a reference range. It is important to recognize that there is no single tap and drill size. For slightly smaller threaded holes, if the torque is too large, you can easily break the tap.
2. Use forming taps as much as possible
Forming tap is a chip free machining process that involves extruding the processed material into shape. The most common reason for taps is that they are blocked by their own chips, and this squeezing of the tap is impossible. The rolling tap also has a larger cross-sectional area, so the tap itself is stronger than the cutting tap.
Forming taps have two drawbacks. Firstly, it cannot be used for materials with high hardness up 42HRC. Secondly, some industries do not allow the use of forming taps because the processing process may create voids that trap pollutants on the threads. Form tapping can also cause an increase in stress on the thread.
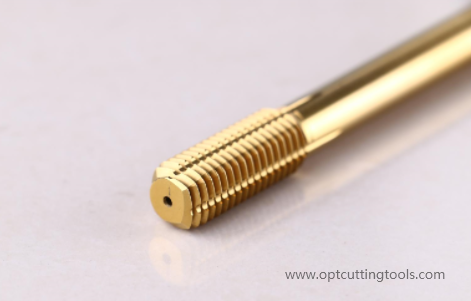
3.Using other cutting tool making threads
For difficult machining materials or high value-added component, thread milling cutters can be used instead of tapping.
The service life of thread milling cutters is longer than that of taps, although the cutting speed of thread mills is slower. You can mill threads closer to the bottom of the blind hole, and a single thread milling cutter can process threads of various sizes. In addition, thread milling cutters are more suitable for processing materials that are harder than taps.
For materials exceeding 5.0 HRC, thread milling cutters may be the only option. Moreover, if the thread mills accidentally breaks into the workpiece, it can be easily removed. The thread milling cutter has a smaller hole than the machined part, so it will not break into the part like a tap, which is difficult to handle
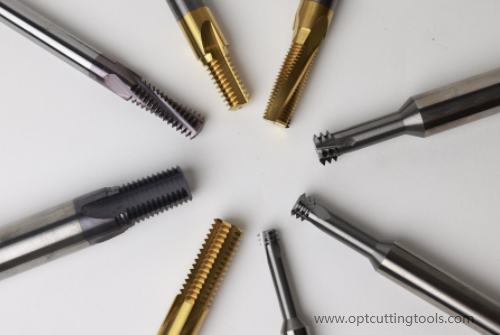
4. Use spiral flute taps in blind hole
If you are processing blind holes, the inability to remove chips may be the most common cause of tap breakage. Iron filings are discharged upwards,that's why we use spiral flute taps, . In addition, please note that spiral flute taps are not as impact-resistant as more common tip taps and are recommended for blind hole machining.
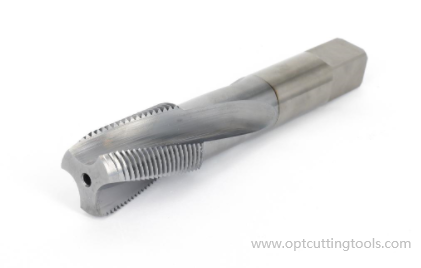
5. Pay attention to the threading depth
When machining blind holes, our suggestion is to pay attention to the depth of the blind hole.
Hitting the tap to the bottom of the blind hole will almost certainly break the tap. Many people are unaware of this, so you need to calculate how much clearance should be left at the bottom.
6. Choose to use a special tapping lubricant
Most machine coolants, especially water-soluble coolants, are not suitable for tapping because the lubricity of oil is relatively better than that of water.
If you encounter processing problems, please try using a special tapping lubricant. Place it next to the machine tool, fill it with a container, and program the G code to automatically immerse the tap into the cup. Alternatively, you can try coating taps to increase lubrication through coating.
7. Use the correct tapping tool handle (recommended only)
Regarding the tapping tool handle. Firstly, use a lock to lock the square handle inside the tapping tool handle, so that it does not rotate in the tool handle. Because tapping requires a lot of torque, having a correct lock on the tool handle is very helpful for tapping. You can use a tap chuck or a special ER tap chuck to achieve this.
Secondly, even if your device supports rigid tapping, consider floating tool handles. Floating tool handles are necessary in the absence of rigid tapping, but even in most rigid tapping situations, they can extend the tapping life. This is because the machine tool is limited by the acceleration of the spindle and shaft, and cannot synchronize the tap with the thread being processed. There is always some axial force pushing or pulling. Floating tool handles can alleviate stress caused by a lack of synchronization.
Overall, the above are 7 main reasons caused tap breakage. Perhaps the points we mentioned cannot fully cover the possibility of tap breakage. Welcome contact us for further discussion your machining.
Post time: Oct-17-2023