In the process of machining, it is often difficult to use standard tools for machining, so the manufacture of non-standard tools is very important for machining.
The use of non-standard tools in metal cutting is often seen in milling, so this paper mainly introduces the manufacture of non-standard tools in milling.
Because the production of standard tools is aimed at the cutting of common metal parts or non-metallic parts with a wide range of surfaces, when the hardness of the workpiece is increased due to overheating treatment, or the workpiece is stainless steel, it is very easy to stick to the tool, and there are also some cases where the surface geometry of the workpiece is very complex, or the machined surface has high roughness requirements, the standard tools can not meet the needs of processing. Therefore, in the process of machining, it is necessary to carry out targeted design for the material of the tool, the geometric shape of the edge, the geometric angle, etc., which can be divided into two categories: special customization and non-special customization.
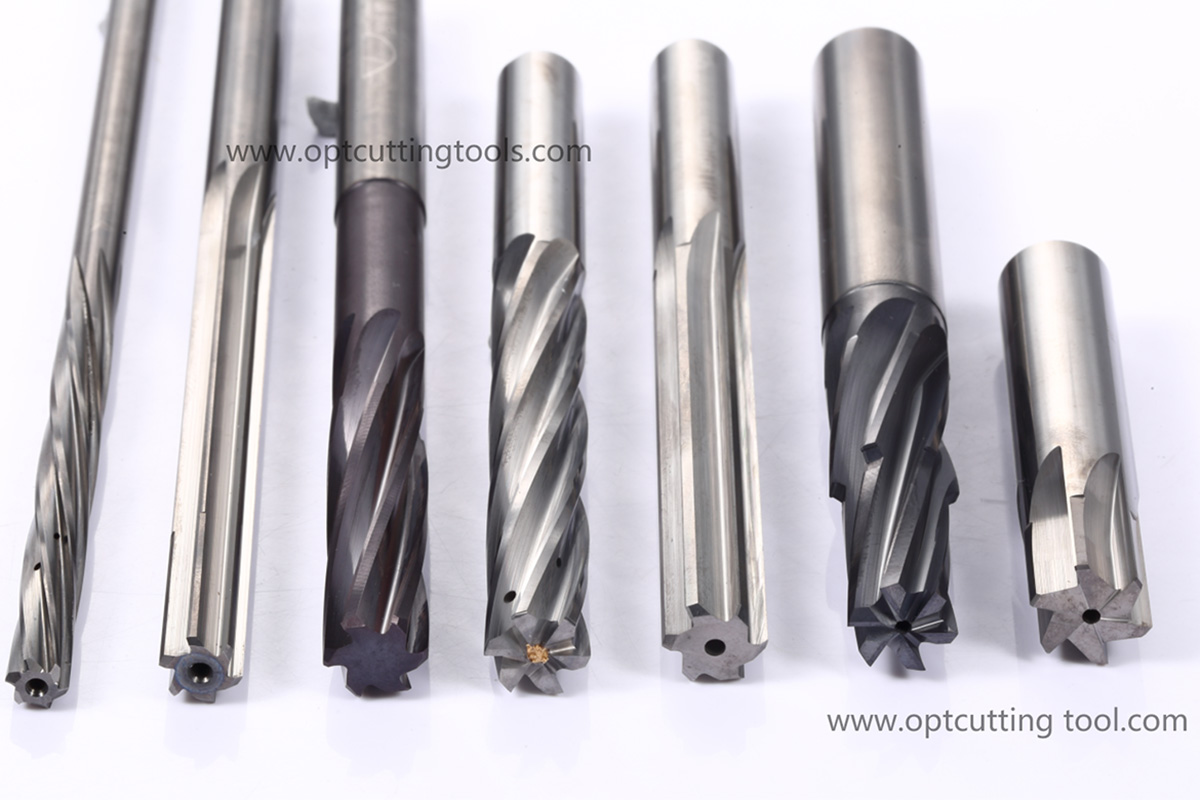
I.Non-customized tools mainly solve the following problems: size, surface roughness, efficiency and cost
(1). Size problem.
You can select a standard tool with a size similar to the required size, which can be solved by change grinding, but two points need to be noted:
1. The size difference should not be too large, generally not more than 2mm, because if the size difference is too large, it will cause the groove shape of the tool to change, and directly affect the chip space and geometric angle;
2. If the end milling cutter with edge hole can be grinded on the ordinary machine tool, the cost is lower. If the keyway milling cutter without edge hole cannot be grinded on the ordinary machine tool, it needs to be grinded on the special five-axis linkage machine tool, and the cost will be higher.
(2). Surface roughness.
This can be achieved by changing the geometric angle of the edge. For example, increasing the degree of the front and rear angles will significantly improve the surface roughness of the workpiece. However, if the machine tool of the user is not rigid enough, it is possible that the blunt edge can improve the surface roughness instead. This aspect is very complex, and the conclusion can only be drawn after the analysis of the processing site.
(3). Efficiency and cost issues
Generally, non-standard tools can mix several processes into one tool, which can save tool change time and processing time, and greatly improve output efficiency! Especially for parts and products processed in batches, the cost saved is far greater than the cost of the tool itself;
II The tools that need to be customized are mainly to solve three problems: special shape, special strength and hardness, and special chip holding and chip removal requirements.
(1). The workpiece to be processed has special shape requirements.
For example, lengthen the tool required for machining, add the end tooth reverse R, or have special taper angle requirements, handle structure requirements, edge length dimension control, etc. If the shape requirements of this type of tool are not very complex, it is still easy to solve. The only thing to be noted is that the processing of non-standard tools is relatively difficult. Therefore, the user should not excessively pursue high accuracy if it can meet the processing requirements. Because high precision itself means high cost and high risk, which will cause unnecessary waste to the production capacity and cost of the producer.
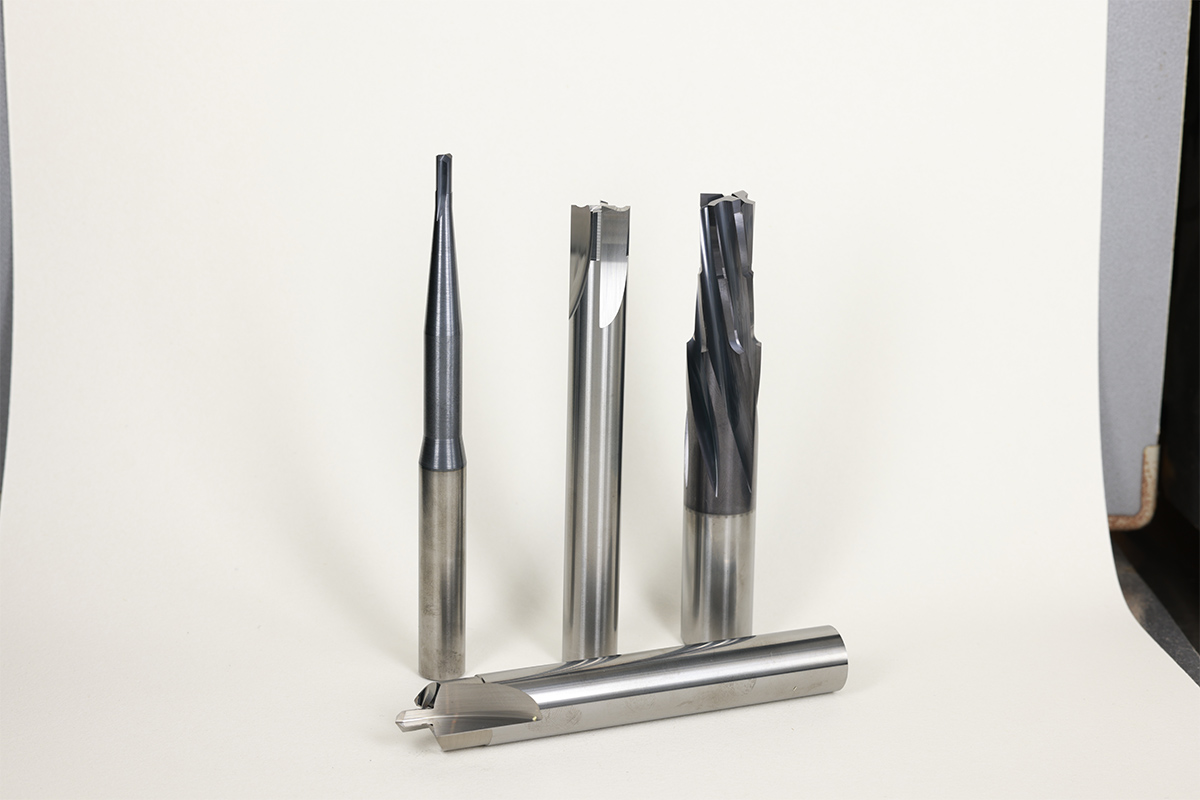
(2). The processed workpiece has special strength and hardness.
If the workpiece is overheated, the strength and hardness are high, and the general tool material cannot be cut, or the tool adhesion is severe, which requires special requirements for the tool material. The general solution is to select high-grade tool materials, such as cobalt-containing high-speed steel tools with high hardness to cut quenched and tempered workpiece materials, and high-quality cemented carbide tools can be used to process high-hardness materials, and even milling can be used instead of grinding. Of course, there are also some special cases. For example, when processing aluminum parts, there is a kind of tool called superhard tool on the market, which is not necessarily suitable. Although aluminum parts are generally soft and can be said to be easy to process, the material used for superhard tool is actually an aluminum high-speed steel. This material is indeed harder than ordinary high-speed steel, but it will cause affinity between aluminum elements when processing aluminum parts, Make the tool wear worse. At this time, if you want to get high efficiency, you can choose cobalt high-speed steel instead.
3. The workpiece to be processed has special requirements for chip holding and chip removal.
At this time, a smaller number of teeth and a deeper chip holding groove should be selected, but this design can only be used for materials that are easier to process, such as aluminum alloy. There are many problems to be noticed in the processing
design and processing of non-standard tools: the geometric shape of the tool is relatively complex, and the tool is prone to bending, deformation, or local stress concentration during heat treatment. Therefore, attention should be paid to avoid the parts prone to stress concentration during design, and for the parts with large diameter changes, bevel transition or step design should be added. If it is a slender piece with large length and diameter, it needs to be checked and straightened every time it is quenched and tempered in the heat treatment process to control its deformation and runout. The material of the tool is brittle, especially the hard alloy, which makes the tool break when encountering large vibration or processing torque in the process. This usually does not cause great damage in the process of using conventional tools, because the tool can be replaced when it is broken, but in the process of using non-standard tools, the possibility of replacement is small, so once the tool breaks, A series of problems, such as delayed delivery, will cause great losses to the user.
All of the above are aimed at the tool itself. In fact, the manufacturing of non-standard tools is not so simple. This is a systematic project. The experience of the design department of the producer and the understanding of the processing conditions of the user will affect the design and production of non-standard tools. The processing and detection methods of the production department of the producer will affect the accuracy and geometric angle of non-standard tools. The repeated return visits, data collection and information of the sales department of the producer will also affect the improvement of non-standard tools, which will play a decisive role in the success of the user in using non-standard tools. Non-standard tool is a special tool produced according to special requirements. Choosing a manufacturer with rich experience will save a lot of time and energy for the user.
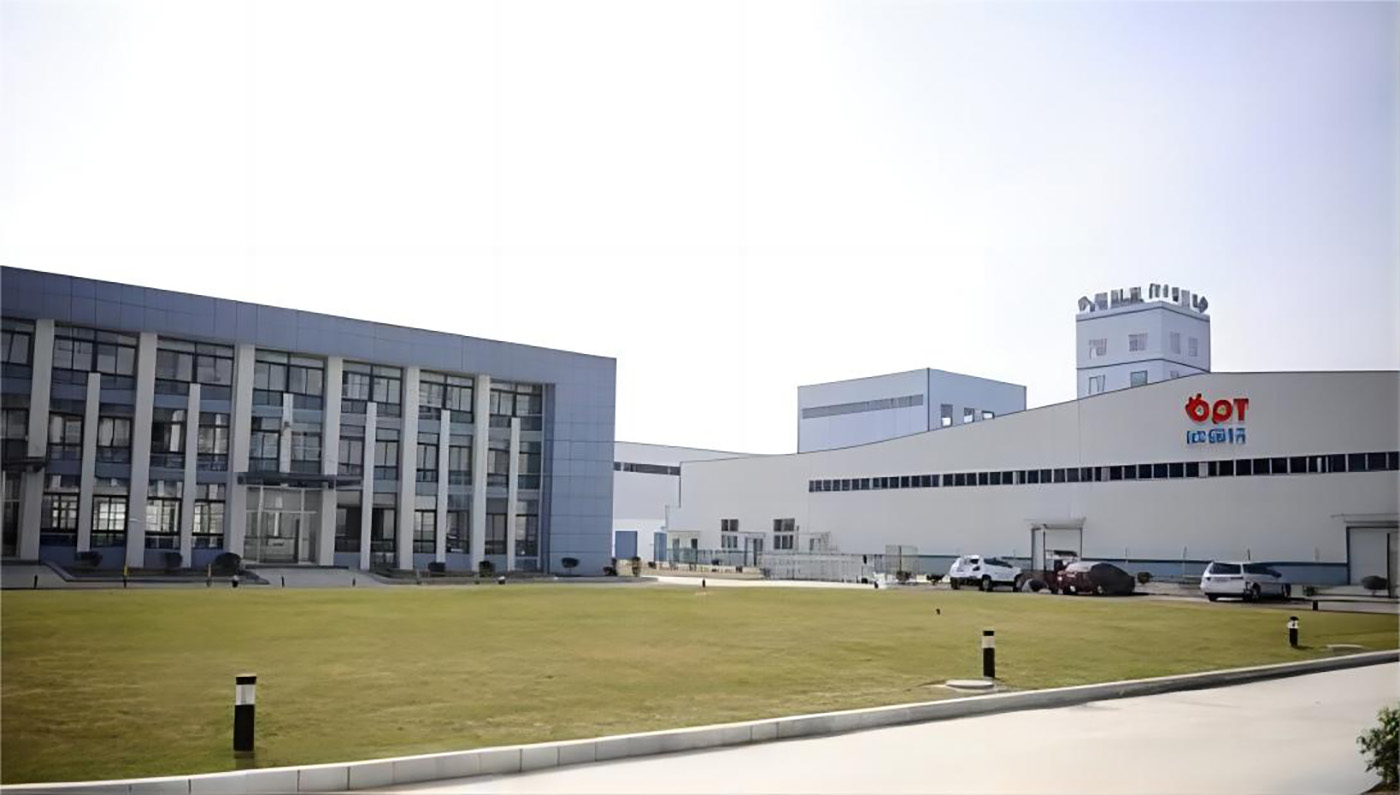
Post time: Feb-23-2023